CONCRETE CANCER – A $13 BILLION PROBLEM
Concrete cancer is a significant issue in Australia, costing billions of dollars in infrastructure repairs annually.
The problem stems from a material known as rebar, which is the steel bar and mesh used to provide strength and reinforcement in concrete infrastructure such as bridges, wharfs, jetties, sewer tanks, and buildings.
The steel rebar that engineers traditionally rely on is prone to corrosion, expanding many times over with cracking and spalling of the concrete. This ‘concrete cancer’ weakens the concrete from the inside, significantly shortening these structures’ lifespans at great taxpayer expense.
Beyond the financial burden, it also has a devastating environmental impact. Cement production is responsible for 8% of the world’s carbon emissions, while the construction industry accounts for 50% of the world’s natural resource extraction and landfill. The frequent maintenance and replacement of concrete structures due to corrosion only exacerbates this issue. As Australia prepares for an infrastructure boom, it is crucial to address the problem of concrete cancer and find ways to preserve and reinforce our infrastructure in a more sustainable and long-lasting manner.
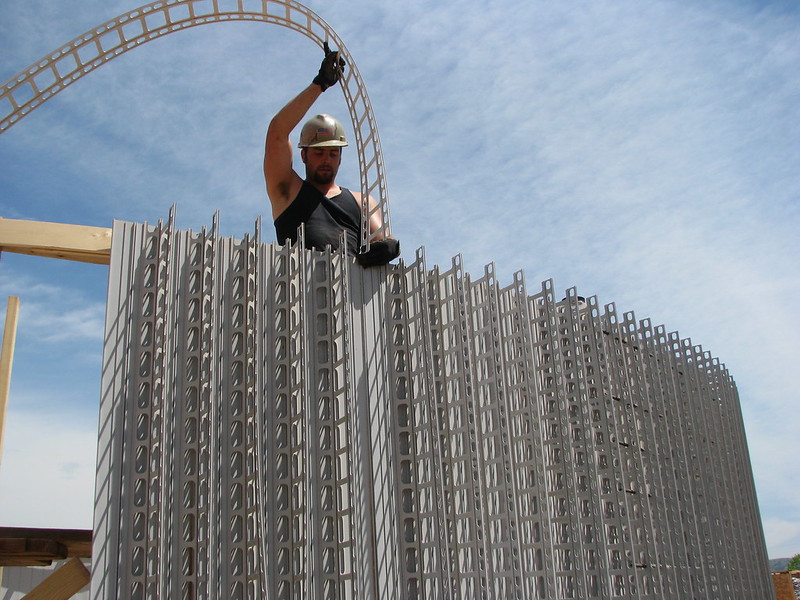
INCONMAT’S INNOVATIVE SOLUTION
Inconmat has addressed this problem at the root cause with a code compliant rebar alternative to steel rebar. Tuf-Bar is made from Fibre Reinforced Polymer (GFRP), a material that will never rust or corrode.
Tuf-Bar means the longevity of concrete infrastructure is no longer reliant on the rebar, and it is already changing the face of the industry. Previously, a minuscule 1% of bridges have met their design life due to corrosion of their rebar. They have also had a relatively short maintenance life; lasting only 20 to 30 years before requiring repairs.
Tuf-Bar is creating a new normal, where infrastructure is expected to last 100 years without maintenance, and have a 200-year to infinite design life. With this new approach, the bridges of today could still be comfortably functioning in the 23rd or 24th century.
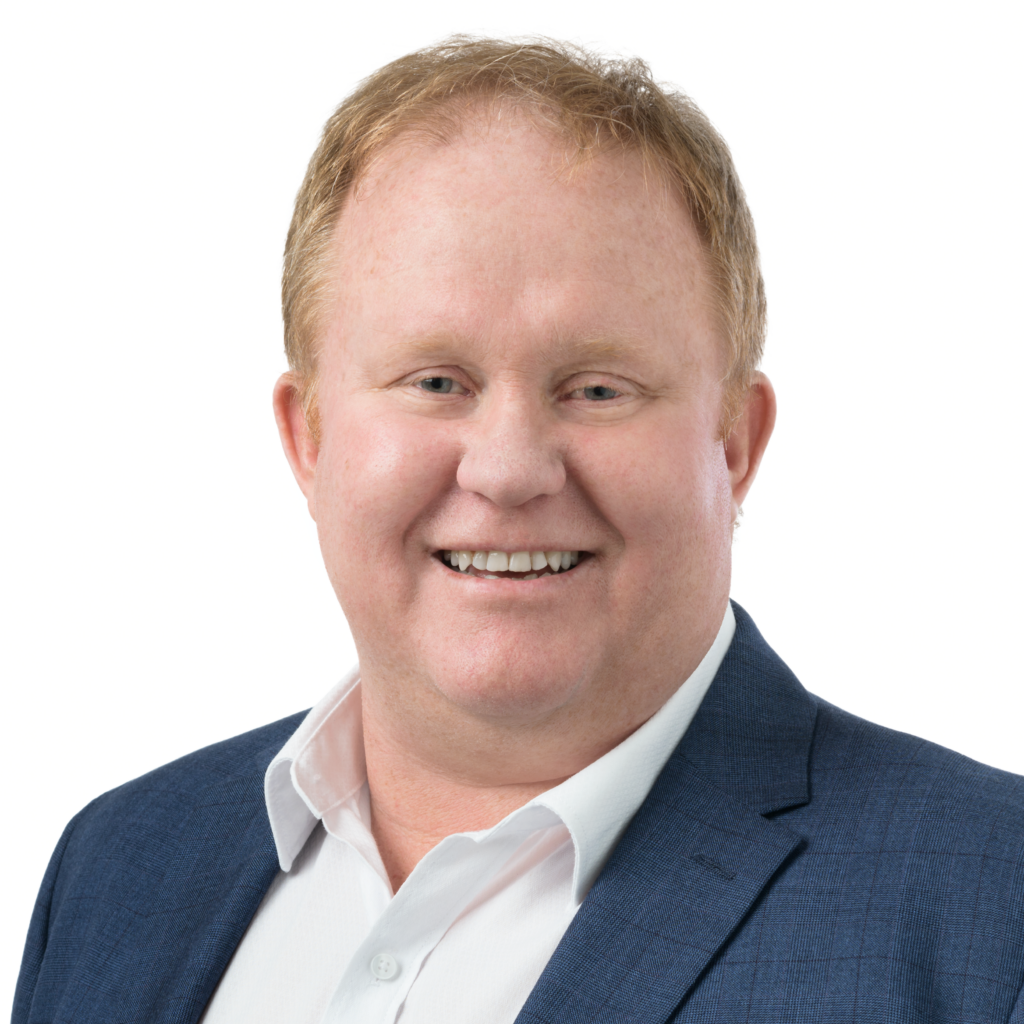
ORIGIN
Inconmat was founded by Darren Lutze in 2009, after his previous experience in the construction industry drove him to find a better way to reinforce and maintain Australia’s infrastructure.
Darren’s primary mission is to improve sustainability of the sector: “We are now all too aware of the construction sector’s impact on the environment, and the world is at a point where we must change.”
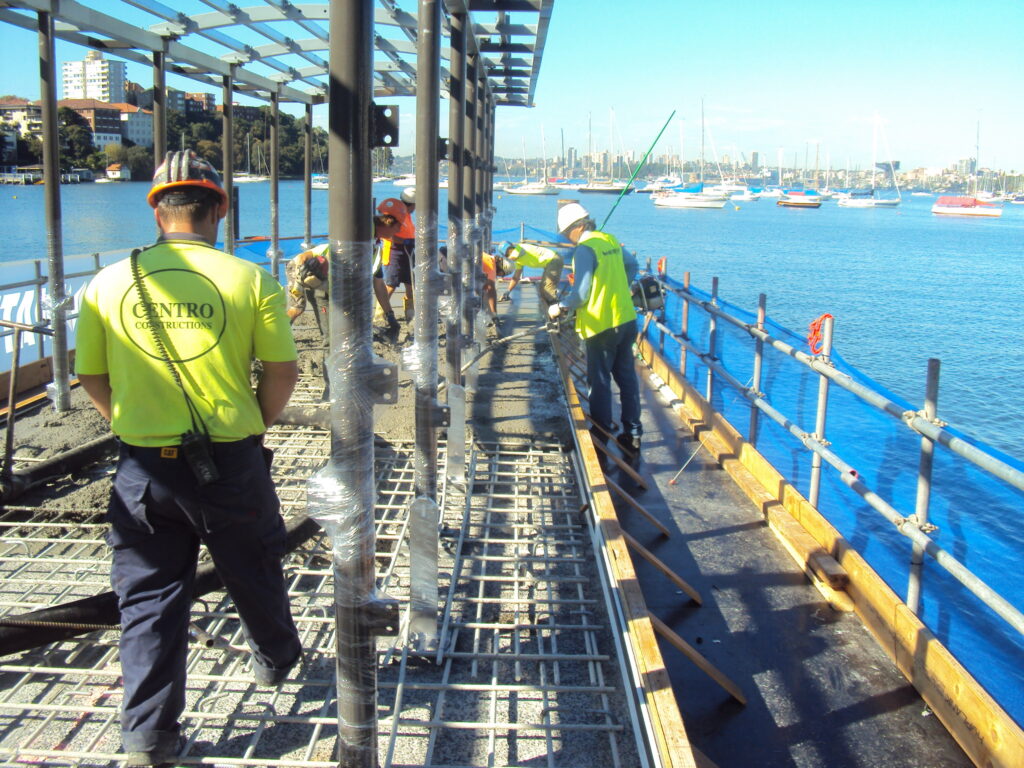
BUILT THROUGH EDUCATION
In a traditionally risk-averse industry Inconmat initially faced challenges in gaining acceptance of GFRP rebar in the engineering community. As a result, they have dedicated a significant amount of time to education, working closely with all three South Australian universities and the University of Southern Queensland. They are also currently working with the Queensland Department of Main Roads and Transport in order to support the state’s transition to climate resilient infrastructure.
Inconmat has also developed and released the world’s only GFRP rebar design software so that engineers can comfortably design with Tuf-Bar in the same way they design with steel rebars.
Darren says that uptake has accelerated in recent years: “There are now enough GFRP rebar-based projects in the country for people to have confidence in its effectiveness.”
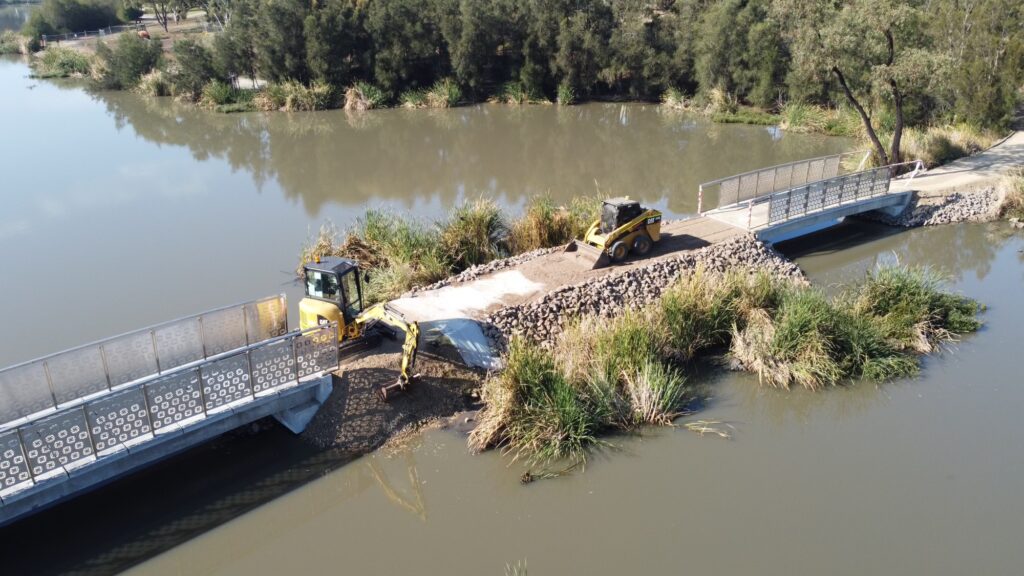
HISTORY-MAKING PROJECTS
Inconmat’s commitment to collaboration has seen them involved in several world-first projects. They recently partnered with Rocla to create the world’s first glass fibre reinforced geopolymer bridge for the City of Greater Geelong. This collaboration was recognized by the IPWEA (Institute of Public Works Engineering Australia) with three awards in innovation, environmental sustainability, and public works.
Tuf-Bar has also made history by being the first GFRP rebar used in the construction of a multi-storey building, in the University of Wollongong’s new cutting-edge research facility.
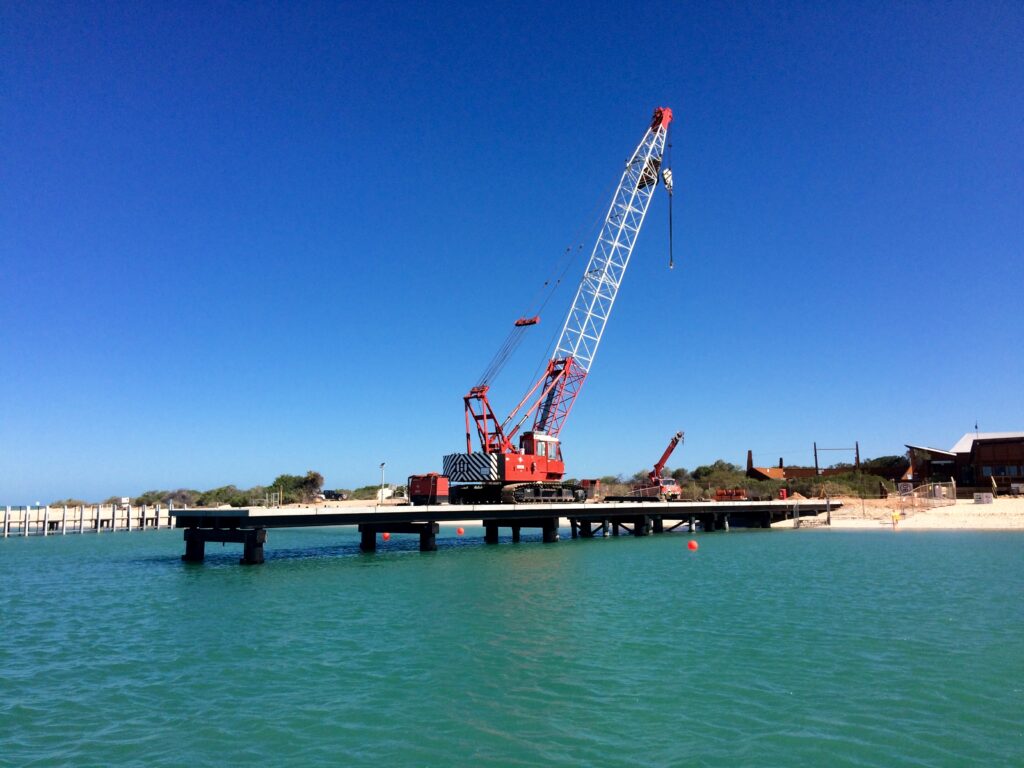
FUTURE FOCUS
Inconmat will soon be transitioning to a local manufacturing model in South Australia. The new manufacturing plant will employ around 20 people, and its Adelaide location means Inconmat can situate itself in the centre of its Australia-wide customer base.
Inconmat has several other exciting future developments. This includes swapping out their vinylester resins to Change Climate Bio Epoxy resin, which is the world’s first 100% BPA-free bio-resin. This will have further positive impact on the long-term sustainability of their products.
Inconmat is also heavily involved in the creation and construction of large-scale anaerobic digestion plants, which convert food waste to energy.
For Darren, Inconmat’s purpose goes far beyond sustainable infrastructure. “I look at this work as playing a part in custodianship for future generations. To quote the Greek proverb: ‘A society grows great when old men plant trees, the shade of which they know they will never sit in.’ Doing something because it’s the way it’s always been done isn’t a good enough reason anymore. We have to change for the better.”