In the heart of innovation, within Princeton University, a remarkable journey began that will soon redefine the landscape of lithium-ion battery recycling. Founded in 2019, Princeton NuEnergy (PNE) embarked on a mission to revolutionize the way we view, handle, and recycle critical materials throughout all stages of battery production and life. At the core of PNE’s vision lies a groundbreaking patented surface treatment technology, the Low-Temperature Plasma-Assisted Separation (LPAS™) process. This offers a uniquely sustainable and cost-effective solution to a global recycling problem.
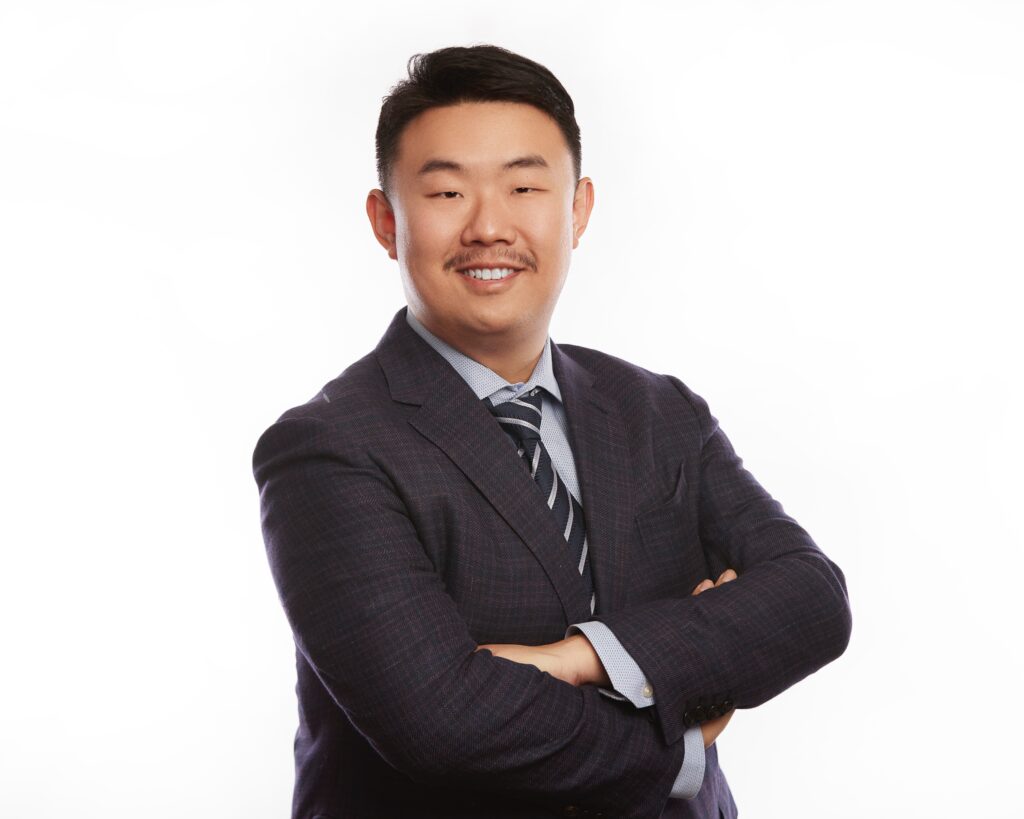
THE BIRTH OF AN ECO-FRIENDLY VISION
PNE’s journey began with fundamental goals of reducing waste and costs associated with traditional lithium-ion battery recycling processes. Two forms of battery waste exist — waste is produced during manufacturing (referred to as scrap), as well as at end-of-life – when batteries are no longer appropriate for their application. Lithium-ion batteries power our modern-day world. Unfortunately, handling of manufacturing scrap and ultimately battery disposal results in ecological harm and the loss of precious resources. Conventional recycling approaches involve high temperature smelting or acid-leaching treatments that damage cathode materials and produce considerable toxic waste as they reduce high value batteries to elemental nickel, cobalt, lithium and other products which must be rebuilt from scratch to create new batteries.
In contrast, PNE’s LPAS™ process not only reclaims and repairs cathode material at all stages of production and throughout the battery’s life cycle, but it can also accomplish this at a significantly reduced cost and with far less waste compared to its counterparts. This is because the rejuvenated cathode material is directly used as input to new batteries, and it is never reduced to elemental form. PNE’s technology and the advanced manufacturing techniques it represents will play a pivotal role in helping the United States retain control over critical materials by enabling cost effective and fully domestic manufacturing processes.
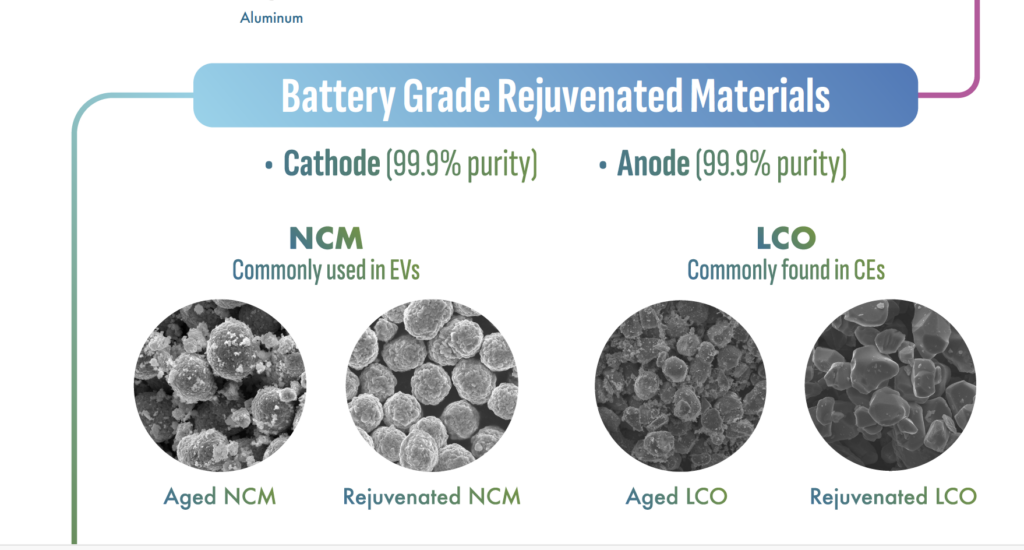
LEADING THE CHARGE: PNE’S INNOVATION TAKES FLIGHT
In late 2022 Princeton NuEnergy launched the first-ever U.S. end-to – end lithium-ion battery direct recycling production facility, a truly groundbreaking event, located in McKinney, Texas. This advanced manufacturing facility not only creates quality jobs but also provides proof of PNE’s position as a pioneering force in sustainable technology.
Just a Quick Note:
InnovationsOfTheWorld.com has partnered with Trade License Zone (TLZ) to support global innovators looking to expand internationally. Take advantage of the UAE’s Free Zones—enjoy streamlined setup, low corporate taxes, and a strategic gateway to the Middle East and beyond.
Get Your UAE Free Zone License Fast & Easy!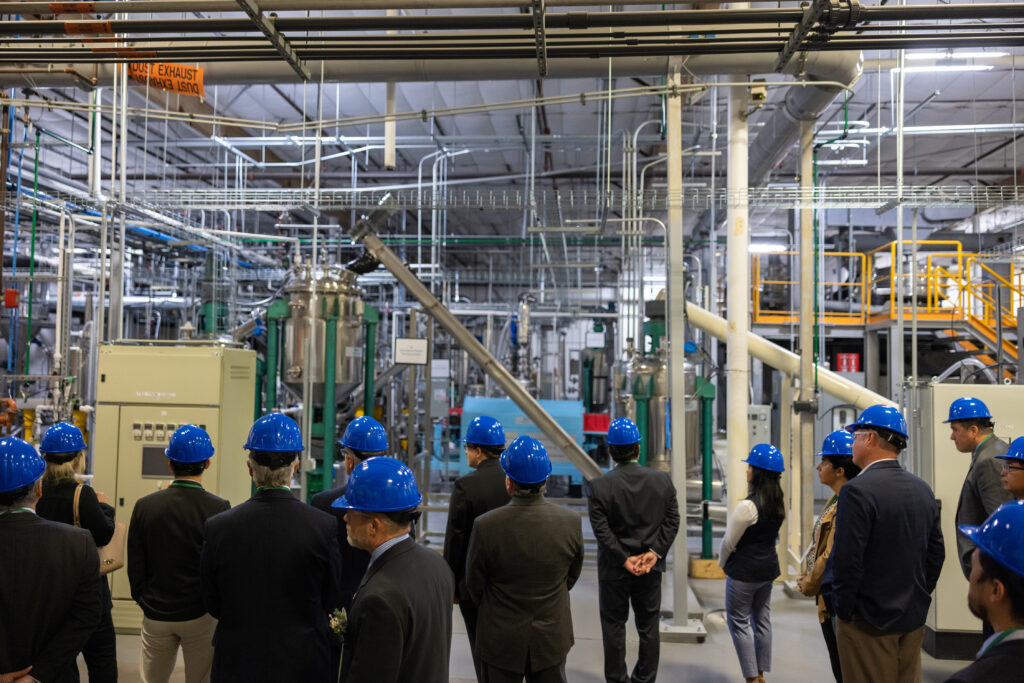
POWERED BY EARLY-STAGE SUPPORT
PNE’s success would not have been possible without the invaluable support it received during its early stages. Organizations like the New Jersey Economic Development Authority (NJEDA), the Commission on Science, Innovation, and Technology (CSIT), the Department of Energy (DOE), and numerous grants including the Small Business Innovation Research (SBIR) STTR Phase I & II, and Energy Efficiency and Renewable Energy (EERE) grants have all played pivotal roles in propelling PNE’s innovative journey.
Moreover, PNE’s successes were further highlighted when it won the CleanTech Open National Grand Prize in 2021. These accomplishments highlight PNE’s relentless pursuit of excellence in recycling.
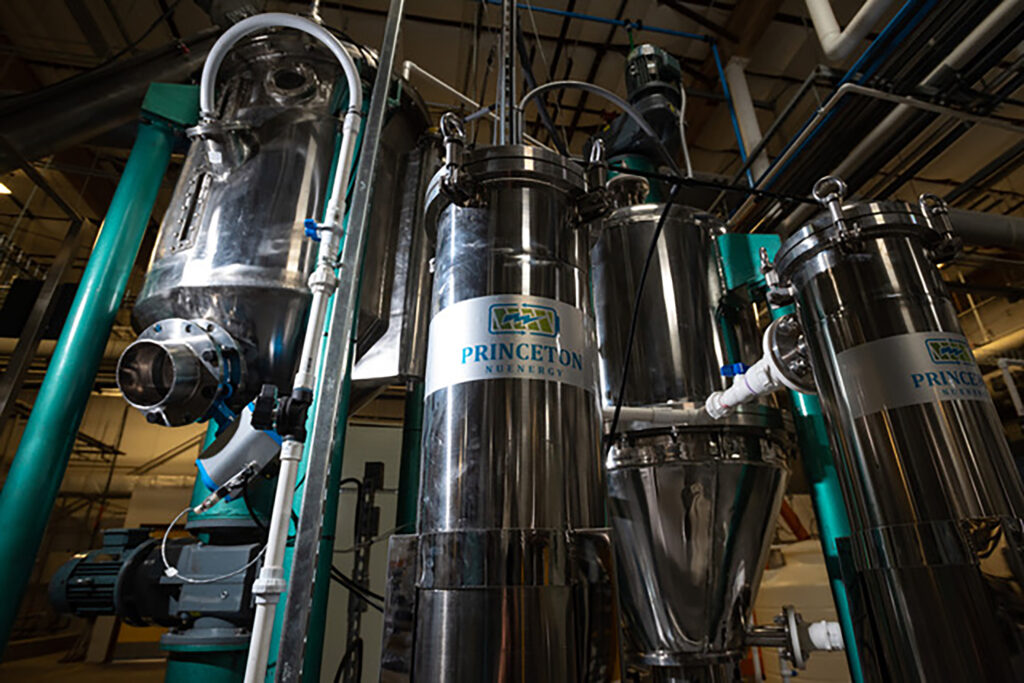
DIRECT RECYCLING: A GAME-CHANGER
Direct recycling represents a fundamental shift in the way we perceive battery materials. Unlike traditional methods that break down materials to their base elements, direct recycling reclaims existing battery materials, offering immediate reuse without additional processing. The advantages include substantial reduction of cost, reduced CO2 emissions, lower energy consumption, and a minimal ecological impact.
Rejuvenated cathode active materials validated by Argonne National Lab and independent OEM testing have demonstrated the effectiveness of direct recycling. Their tests of recycled battery chemistries from PNE such as Lithium Cobalt Oxide (LCO), NCM111, and NCM622, have been proven to have equivalent and in some cases superior extended-life performance to OEM materials during rigorous 1,000 cycle testing. In fact, these same results have shown consistent high performance post-processing for an even wider range of commercially available battery chemistries.
PNE’s dedication to ‘cleaning’ and reclaiming battery materials directly will make a strong and positive impact to environmental sustainability and resource conservation of lithium-ion batteries. The ongoing rigorous testing and assessment with samples from a wide range of customers will continue to validate the viability and superiority of this transformative approach.
A SUSTAINABLE FUTURE WITH PRINCETON NUENERGY
In a world striving for sustainability, Princeton NuEnergy brings its groundbreaking LPAS™ technology and commitment to sustainable battery production and recycling practices. PNE is leading the charge in redefining lithium-ion battery recycling. As PNE embarks on the path of commercializing the first U.S. direct recycling production facility, we anticipate a future where battery waste is minimized, production costs are reduced, and environmental impact is minimized.
In the words of Princeton NuEnergy, “Recycling is no longer just about extracting elements- it’s about reclaiming, revitalizing, and revolutionizing the way we power our world.” PNE’s ground-breaking technology is paving the way towards a brighter, more sustainable future, one recycled battery at a time.