It is incredible to think that in the span of only 125 years the world has been completely transformed by the advent of modern transportation. It has opened the world to travel, commuting to work, moving goods and services in what used to take weeks or even months to a matter of hours, and much of this transformation has been accelerated by suppliers like ZF Group that continue to innovate for greater efficiency and safety.
Today’s mobility industry is increasingly electrified, automated and connected driven by technology and software advances. ZF Group is at the forefront of these mega trends having been a leading developer of transportation solutions for over a century.
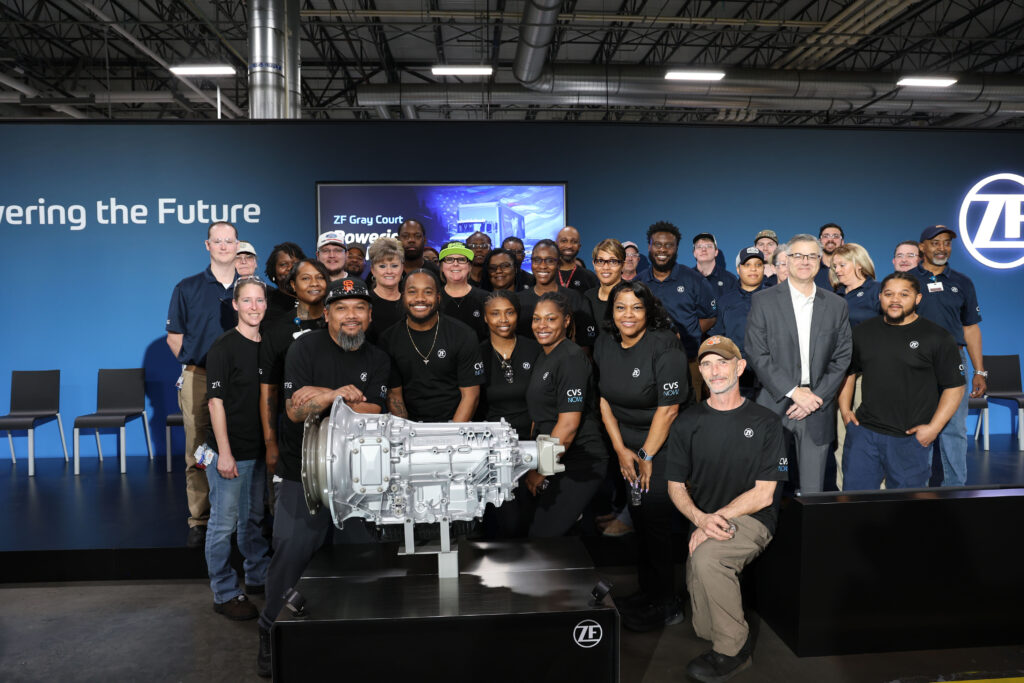
A global leader across ground transportation sectors
ZF is among the three largest global automotive suppliers and is the leading supplier to the commercial vehicle industry globally. It is uniquely positioned to further the industries it serves in four key domains – Electric Mobility, Automated Driving, Vehicle Motion Control and Integrated Safety.
And ZF is accelerating its efforts in all of these areas with state-of-the-art innovations across the spectrum of power train alternatives and advanced driver assistance and automated driving sensing technologies enabling leading edge highway and city driving functions. ZF also combined its chassis systems and active safety systems divisions launching its chassis solutions division with an unparalleled offering of steering, braking and active suspension and its cubiX software. As a top supplier to the global automotive industry, ZF steering and braking products deliver comfort and driving safety into millions and millions of vehicles around the world every day.
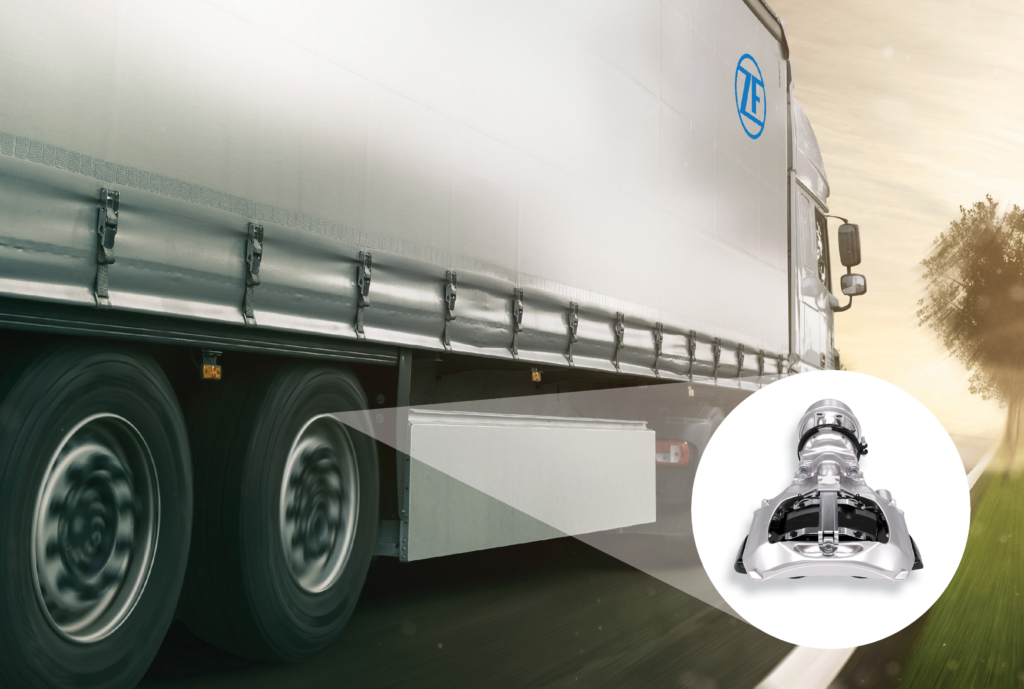
Making the software-defined vehicle a reality
Combining this expertise into holistic solutions that will revolutionize driving in the future, ZF is laying the foundation for the software-defined vehicle that will lead to new functions and features, many that emphasize safety as well as driving comfort. Taking advantage of new digital tools and cloud-based computing to make the mobility experience a more pleasant one for everyone is a major goal at ZF. The development of robust control software plays a critical role in making new electric vehicles more efficient with extended range or combining information from ADAS sensors and Cloud data to anticipate difficult road conditions or a traffic jam around the next corner.
South Carolina a ZF flagship of flex manufacturing for Electric Vehicles
“At ZF our more than 160,000 employees around the globe are focused on clean, safe, comfortable and affordable mobility for everyone, everywhere,” said Ramiro Guttierez, President of ZF North America. “Here in North America, we have nearly 30,000 employees that design, develop and produce some of the most technologically advanced systems found anywhere and these include key locations in South Carolina such as our Gray Court facility that is or soon will produce the full gamut of powertrain variants from internal combustion to plug-in hybrids to full electric for passenger cars and light to medium trucks.”
This establishes Gray Court as ZF North America’s first and premiere flex manufacturing site producing ICE, Hybrid and BEV as well as for light through heavy duty industries. The facility continues to grow and when adding in other ZF facilities in Charleston and Duncan there are over 3,000 employees in the Palmetto state.
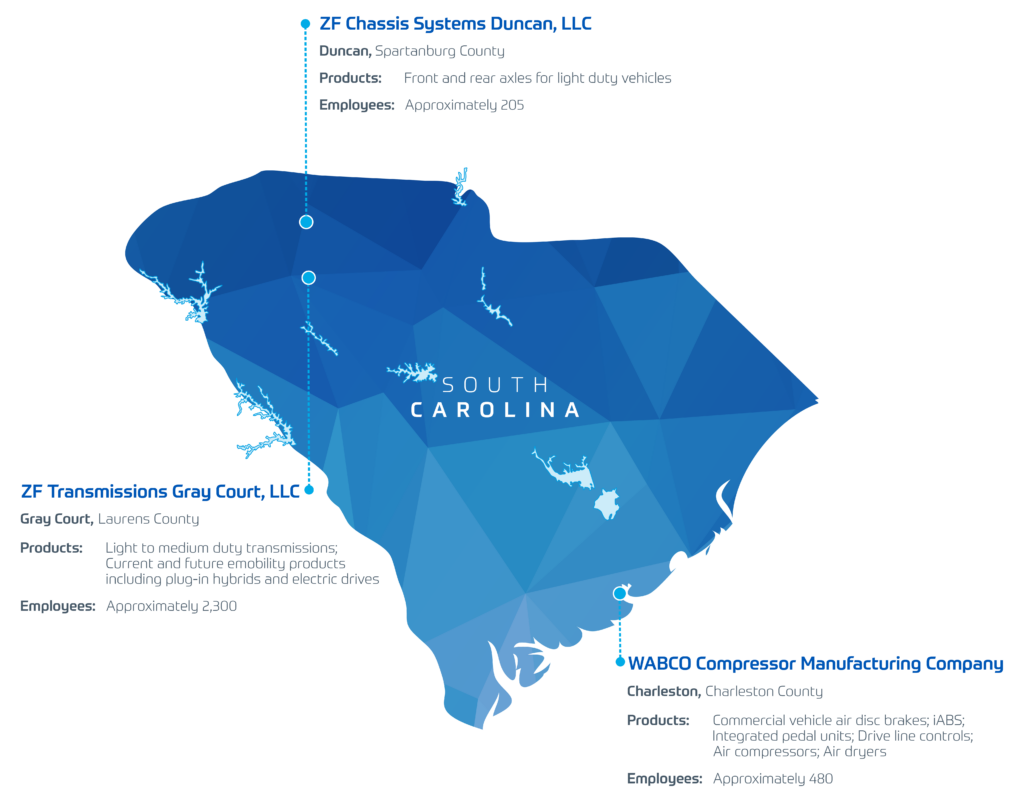
Accelerating growth in the Palmetto state
“South Carolina is an important manufacturing hub for the company and has continued to expand over the past decade to supply technology for this region for both passenger and commercial vehicles,” said Stefan Seeger, vice president and plant manager, ZF Transmission Gray Court. “The future is bright as we launch a new transmissions like the Power Line for large to medium duty pickups and SUVs, and electric vehicle innovations like ZF’s emotor solutions, as well as advanced chassis systems at our locations in Charleston and Duncan.
”This includes sophisticated safety systems such as the air brakes and iABS (anti-lock braking systems) for trucks produced at the Charleston facility. As part of ZF’s dedication to being a full systems supplier for the commercial vehicle market the company purchased WABCO in 2020 to enhance its product portfolio to include advanced braking and related technologies bringing Charleston into the fold. They produce componentry for major truck manufacturers like Daimler, Volvo, Paccar, Navistar, Great Dane and others.
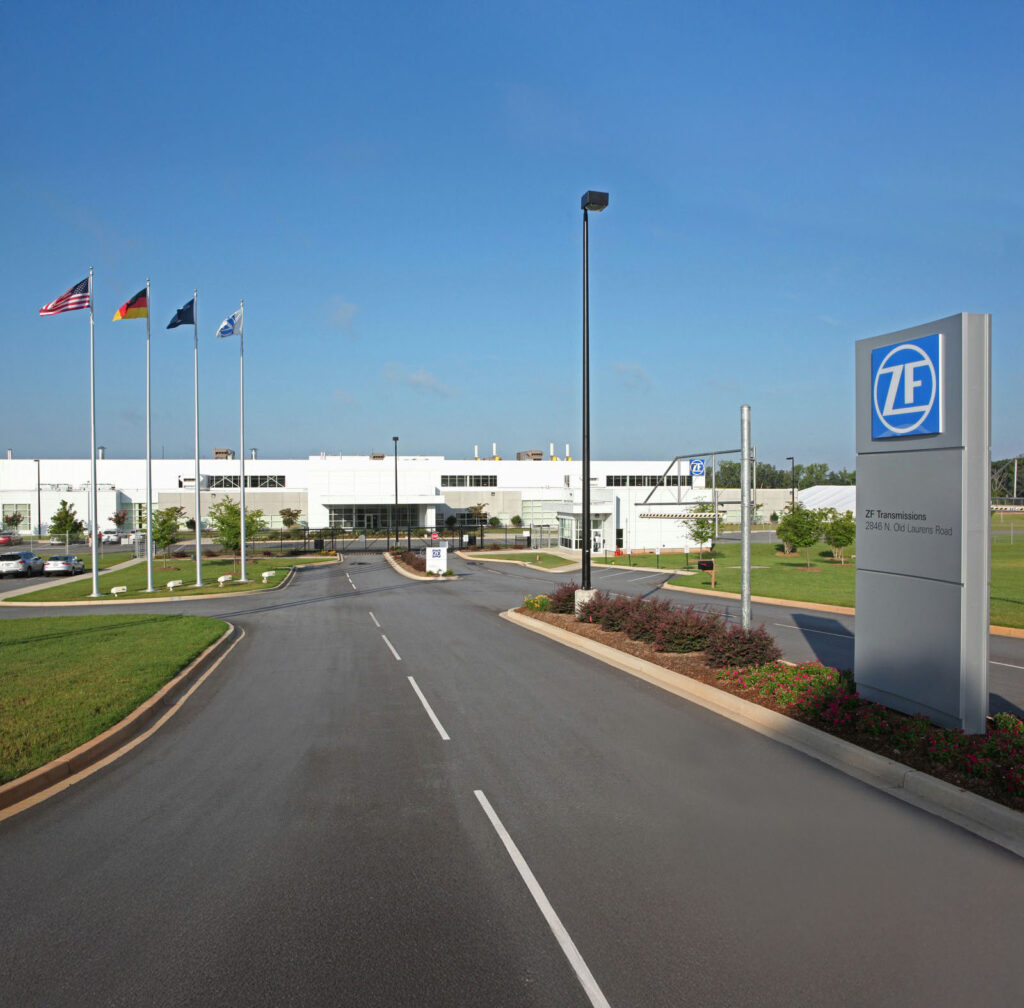
A commitment to communities, the environment and the future
ZF is committed to investing in our communities and in our people. One shining example is the maintenance apprenticeship program that was established in 2018 among partners Piedmont Technical College (PTC), Laurens County Development Corporation (LCDC), Laurens County School Districts 55 and 56, and ZF Transmissions in Gray Court. Also involvement in Sustain SC an the Coordinating Council for Workforce Development (CCWD), and Department of Commerce Education and Workforce Boards and Committees. This program continues to grow and has resulted in an excellent opportunity for students in Laurens County to find good paying jobs while getting their college tuition paid and a pipeline of skilled workers for ZF. Similarly, the locations in Charleston and Duncan are working with the local governments, commerce chambers and school systems to support community programs and educational efforts.
ZF is future oriented, and we are constantly innovating and developing the company to provide Next Generation Mobility solutions to enhance the environment, safety and convenience for people around the globe.
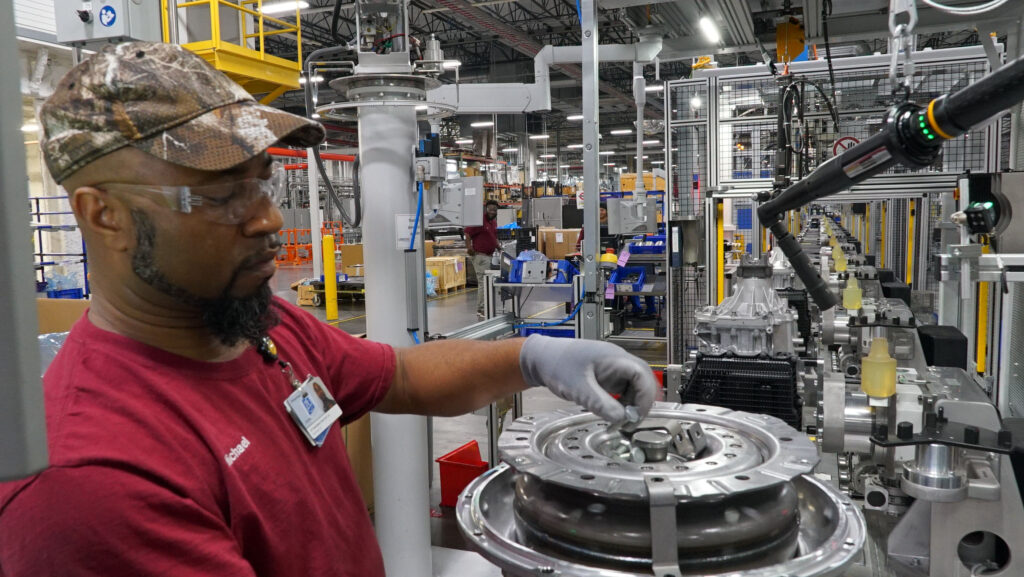
As a globally active technology company, ZF takes on responsibility for environmental sustainability along its entire value chain – for our employees and our locations, as well as in our supply chain and for our products. Thanks to intensive and focused investment in research and development, ZF promotes the topic of sustainable mobility and is embracing sustainably generated energy for its facilities plants at all locations, increasing the energy efficiency of its processes, electrifying a large part of its products, and using recycled materials.