One notable development is the move from internal combustion engines (ICE) to electric vehicles (EVs). The lithium-ion (Li-ion) batteries used in EVs are becoming more prevalent everywhere. These days, they are the go-to choice when it comes to powering everything from mobile phones to power tools, drones, EVs, and more.
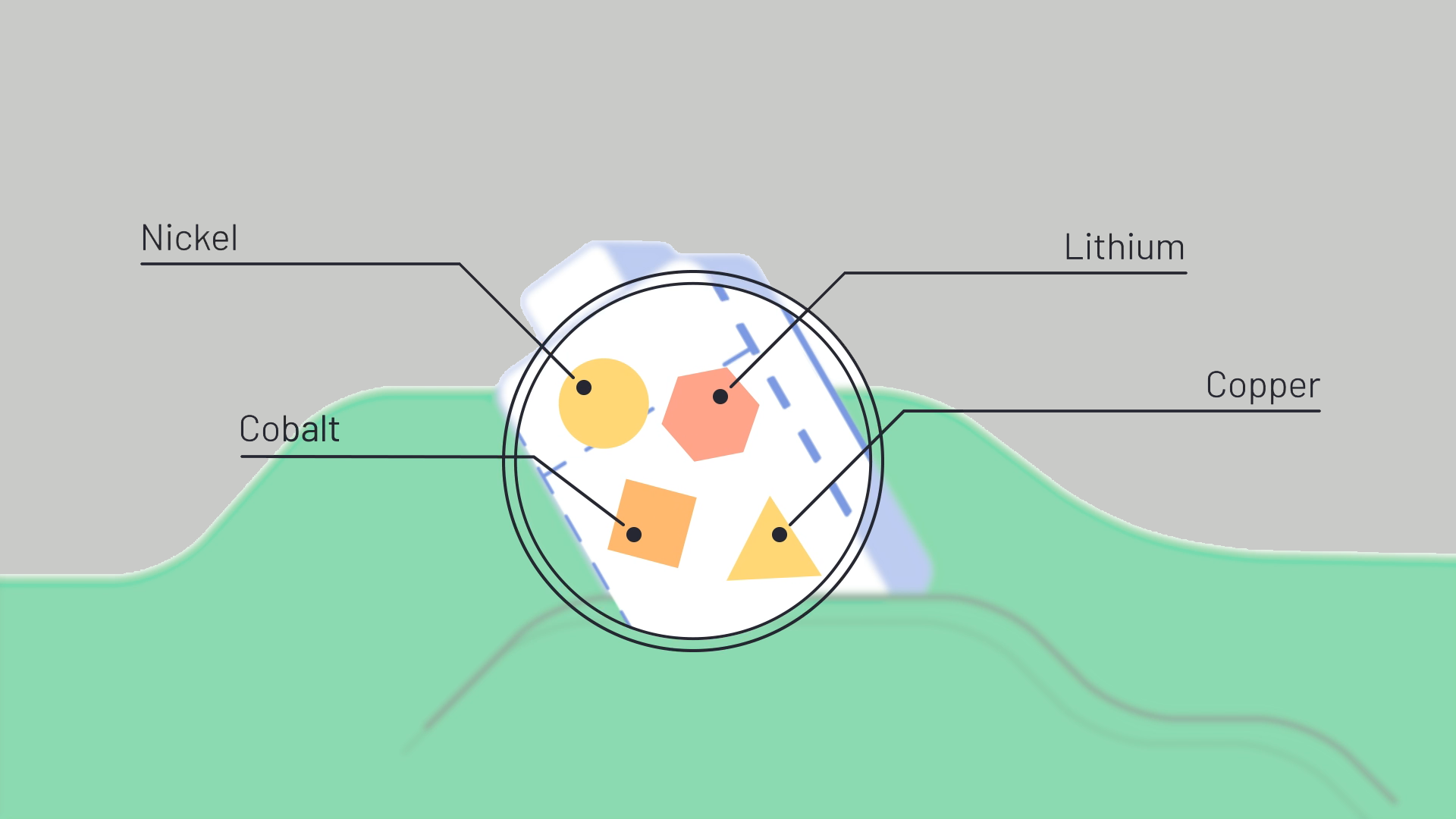
However, mining finite materials – such as lithium, cobalt and nickel – found inside these Li-ion batteries has been associated with pollution, greenhouse gas emissions, and human rights concerns. Using technologies developed in Ontario, Li-Cycle believes it can address many of these pressing environmental issues by creating a sustainable source of these materials for the battery supply chain.
Engineers prize Li-ion batteries for their high-energy density, and because they maintain their capacity for many more charge cycles than other types of batteries. But they don’t last forever. Moreover, every year 500,000 tonnes of lithium-ion batteries are thrown out globally; of these, only a small portion is recycled. This results in a major e-waste problem.
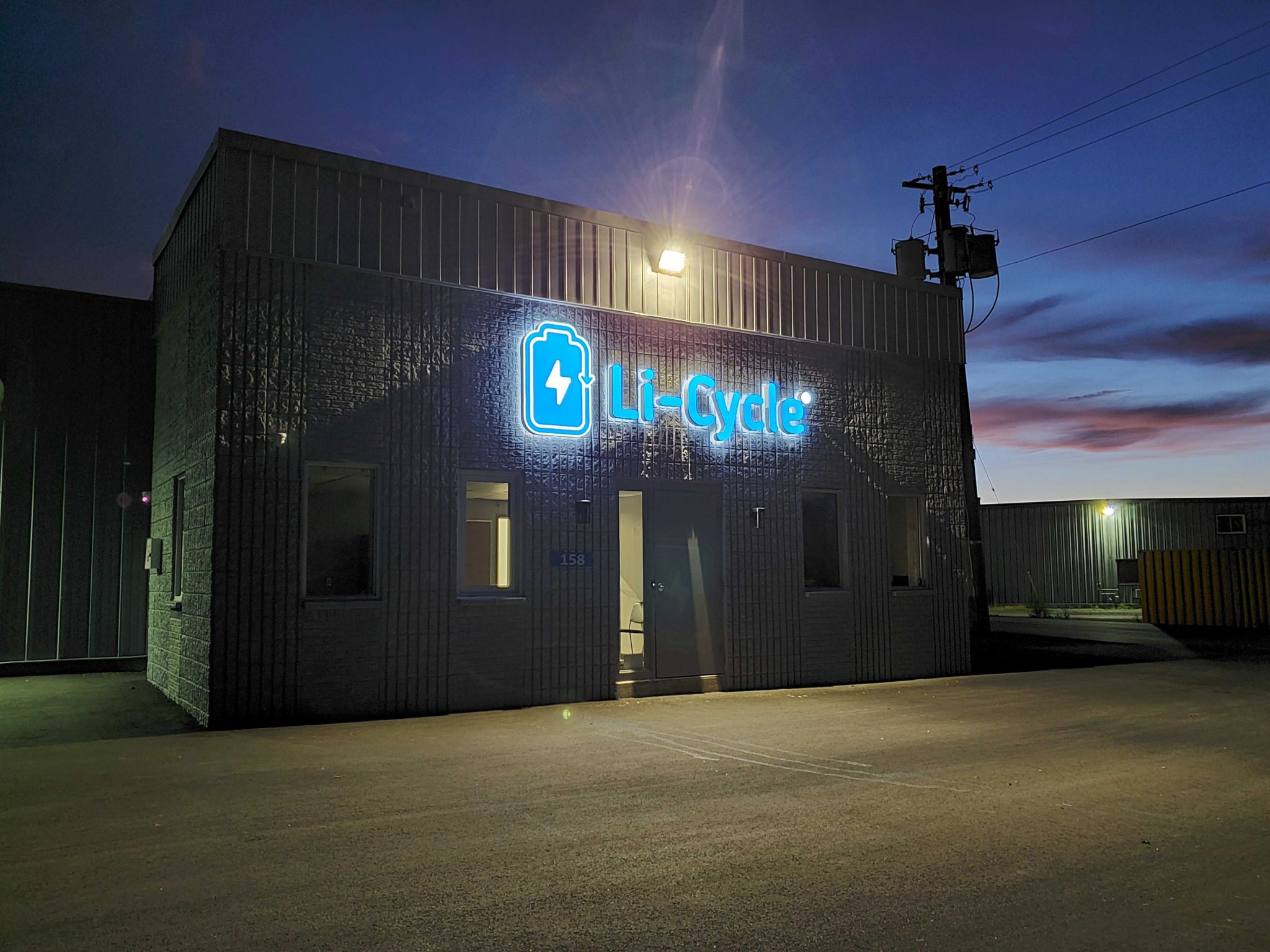
As infrastructure is electrified and energy storage is reimagined, industry experts around the world have committed to working towards creating a “closed loop” for Li-ion batteries.
Just a Quick Note:
InnovationsOfTheWorld.com has partnered with Trade License Zone (TLZ) to support global innovators looking to expand internationally. Take advantage of the UAE’s Free Zones—enjoy streamlined setup, low corporate taxes, and a strategic gateway to the Middle East and beyond.
Get Your UAE Free Zone License Fast & Easy!Li-Cycle is driven to make this vision a reality for all lithium-ion batteries. The company’s Spoke & Hub Technologies™ can sustainably recycle all forms and factors of lithium-ion batteries used in any device – including larger EV batteries – and can recover up to 95% of the materials inside.

End-of-life batteries and battery scrap, generated in battery cell manufacturing, are first taken to Li-Cycle’s Spoke facilities where they are broken down through a submerged shredding process. The process produces plastics, copper, aluminum, and “black mass”, a powder substance which contains lithium, cobalt, nickel, and other metals. Li-Cycle’s Hub facilities will then take the black mass through a hydrometallurgical circuit, or “wet chemistry” recycling process, and convert it into battery-grade materials. From there, the battery-grade materials can be sold to battery cell manufacturers and their supply chain.
With lithium-ion battery usage expected to skyrocket as more and more individuals turn to EVs, recycling Li-ion batteries will be both environmentally essential and an excellent business opportunity.
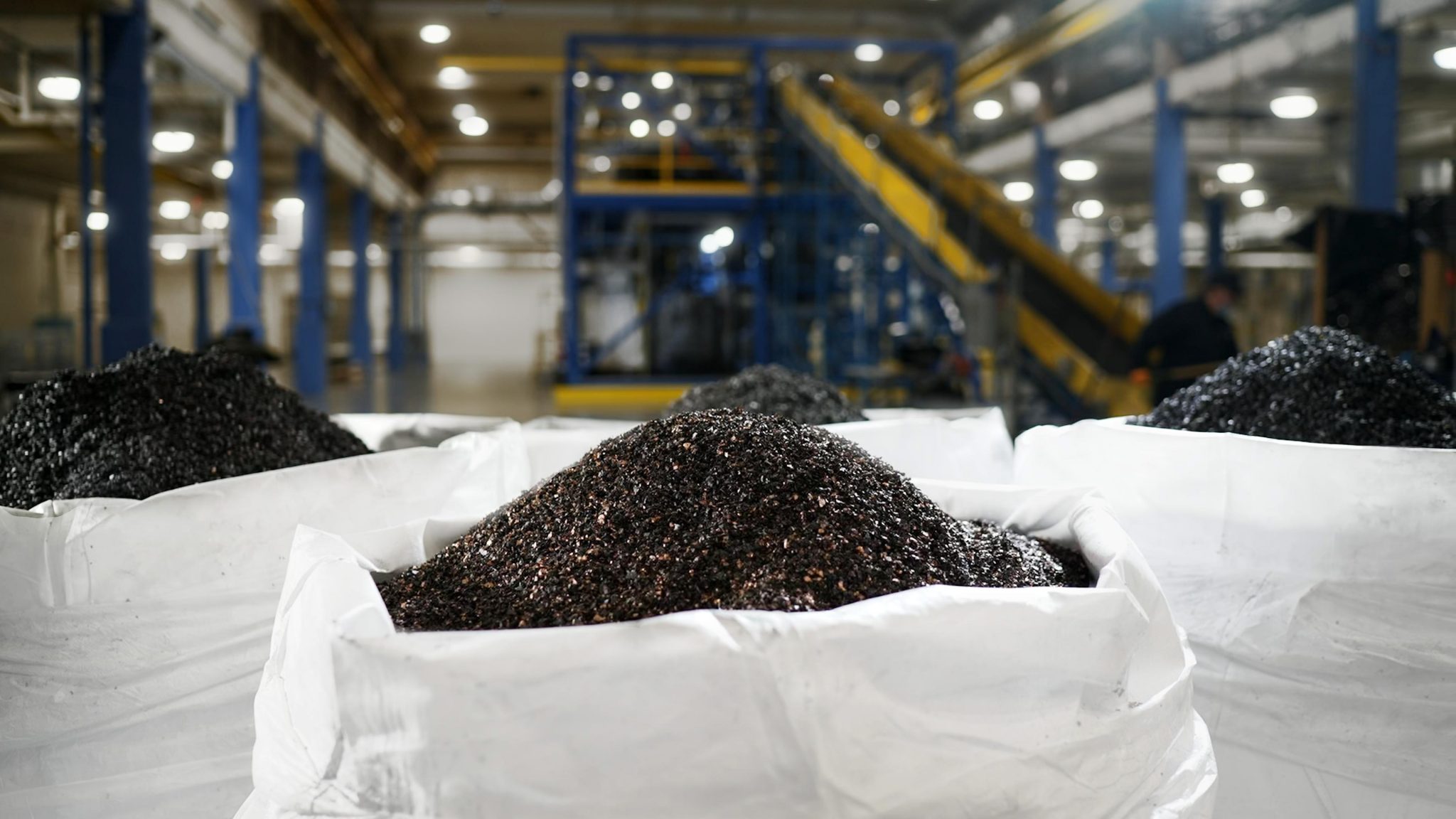
With lithium-ion battery usage expected to skyrocket as more and more individuals turn to EVs, recycling Li-ion batteries will be both environmentally essential and an excellent business opportunity.
Li-Cycle is the largest lithium-ion battery recycling company in North America, with almost 200 employees. The company currently operates two Spoke facilities – one in Kingston, Ontario, the other in Rochester, New York – with the combined capacity of recycling 10,000 tonnes of lithiumion batteries annually. Two further Spokes are under construction in Arizona and Alabama.
The company is also building its first commercial Hub facility in Rochester. Expected to be complete by early 2023, the Hub will be the world’s only recycling plant capable of producing the materials needed to manufacture lithium-ion batteries. By 2025, Li-Cycle anticipates having four operational Hubs and 20 Spokes globally.
While Li-Cycle’s technologies are now patented and commercialized, the company’s co-founders, Ajay Kochhar and Tim Johnston, initially came up with the idea, scribbled on a napkin, in a coffee shop in Toronto. In just five years, the company has grown from an idea (on a napkin) to a commercially operating company. Now publicly traded on the New York Stock Exchange, and with an aggressive expansion plan in place, this proud Canadian company is addressing a key gap in the circular economy.