Virtual reality, real-world enhancements
Looking at the flagship Bombardier Global 7500 jet, your naked eye sees two engines, two wings, a tail and a cockpit. Through the eyes of the thousands of people that design and build them, these jets are more than 35,000 individual parts that make up the most sophisticated business jet ever built.
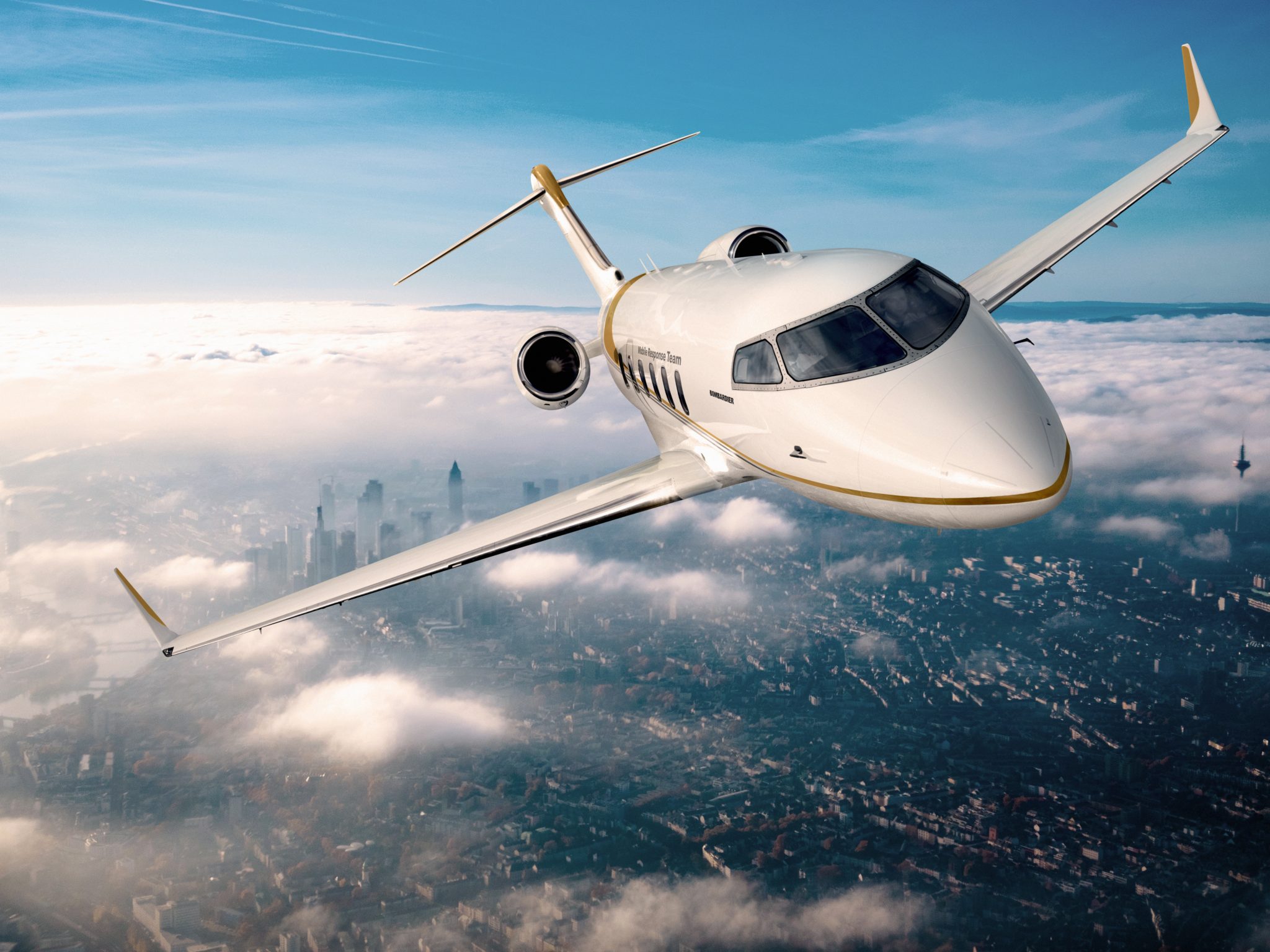
Finding ways to access each part is a key contributing factor to efficiency – when it comes to assembling the aircraft, designing and implementing modifications or in-field service. AI-enhanced augmented and virtual reality is the latest solution in work to address this challenge. It has the potential to drastically change design validations, repair processes and much more as we enter a not-to-distant paperless future, further enhanced by augmented reality in day-to-day tasks.
By leveraging machine-learning for object identification, this technology could soon replace 2D design stations, inspection books, and manufacturing and service workstations. All relevant content will be provided in wearable technology displaying an extended reality environment for the designer, or technician, who can keep hands-free and eyes on the task without referring to a physical manual. This technology could call up tasks and even virtually “point” to where it must be performed.
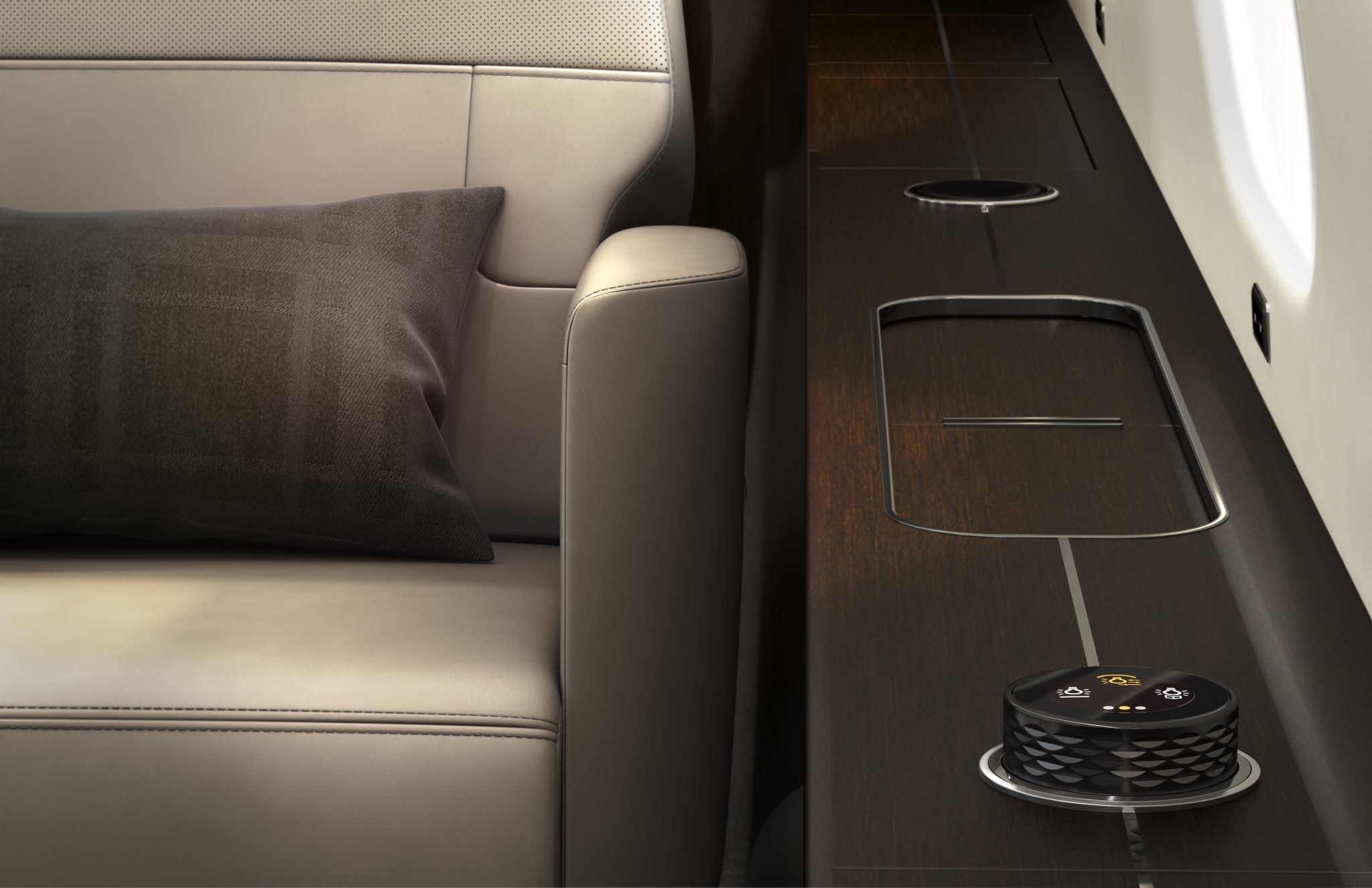
So how do we get there? Researchers are developing an algorithm to translate large CATIA files into smaller, but representative graphics files. After successful file translation, the immersive world will be tested virtually through a proof of concept “walk-through” of a Global 7500 aircraft. The team will then step into a virtual, augmented world building in object recognition capabilities, 3D scanning, anchoring on real aircraft in hangers, followed by the super-position of design data on real-world physical objects.
Ultimately, the augmented reality environment will allow for an on-the-spot comparison of “as-designed” and “as-built,” for use in inspection, repair, and manufacturing – as easily as putting on a pair of glasses.
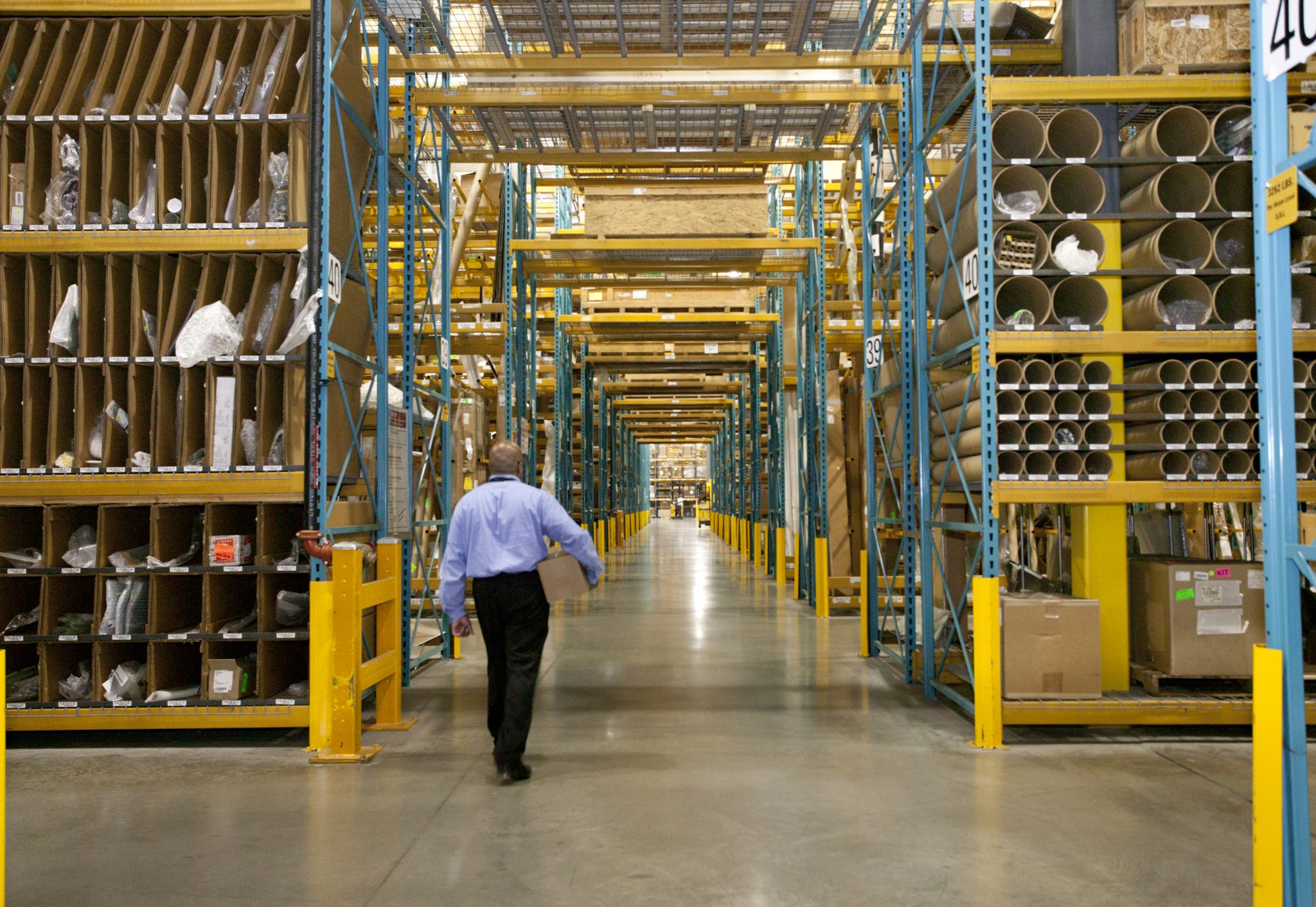
Cutting-edge algorithms predict parts availability
Consistently ensuring parts inventories remain robust throughout the Bombardier service centre network is one of the most important goals for the Service and Support team. Fortunately, help may be on the way thanks to advanced technologies, such as Artificial Intelligence (AI). With the assistance from Scale AI– a consortium of private entities, research centres, and academia providing guidance to Canadian firms to promote the use of AI in industry – Bombardier is embarking on a new research and development project using AI to create advanced algorithms that will investigate new ways to enhance its parts availability process.
The project, spearheaded by Bombardier’s Services and Support Digital Innovations team, is aimed at more effectively monitoring customer parts usage and tendencies to ensure fleet-wide parts are always on the shelves and at the ready.
As part of the initiative, Bombardier will partner with an aircraft maintenance tracking software firm to ensure essential customer parts purchasing and maintenance data is used to build the most accurate algorithms. Utilizing this data, Bombardier will build more robust AI-generated algorithms to effectively predict parts demand and availability.
What makes AI so dynamic? This advanced technology has the capacity to analyze and predict tendencies far beyond what a human can analyze or predict, optimizing the information gathering process. It may also uncover customer purchasing tendencies the Bombardier team didn’t even know it had – such as the ability to predict parts purchasing behaviours across the fleet for a specific time frame, and much more.
While this is the team’s initial foray into utilizing AI, its benefits could ignite further projects – such as nuances in parts distribution processes, and more.
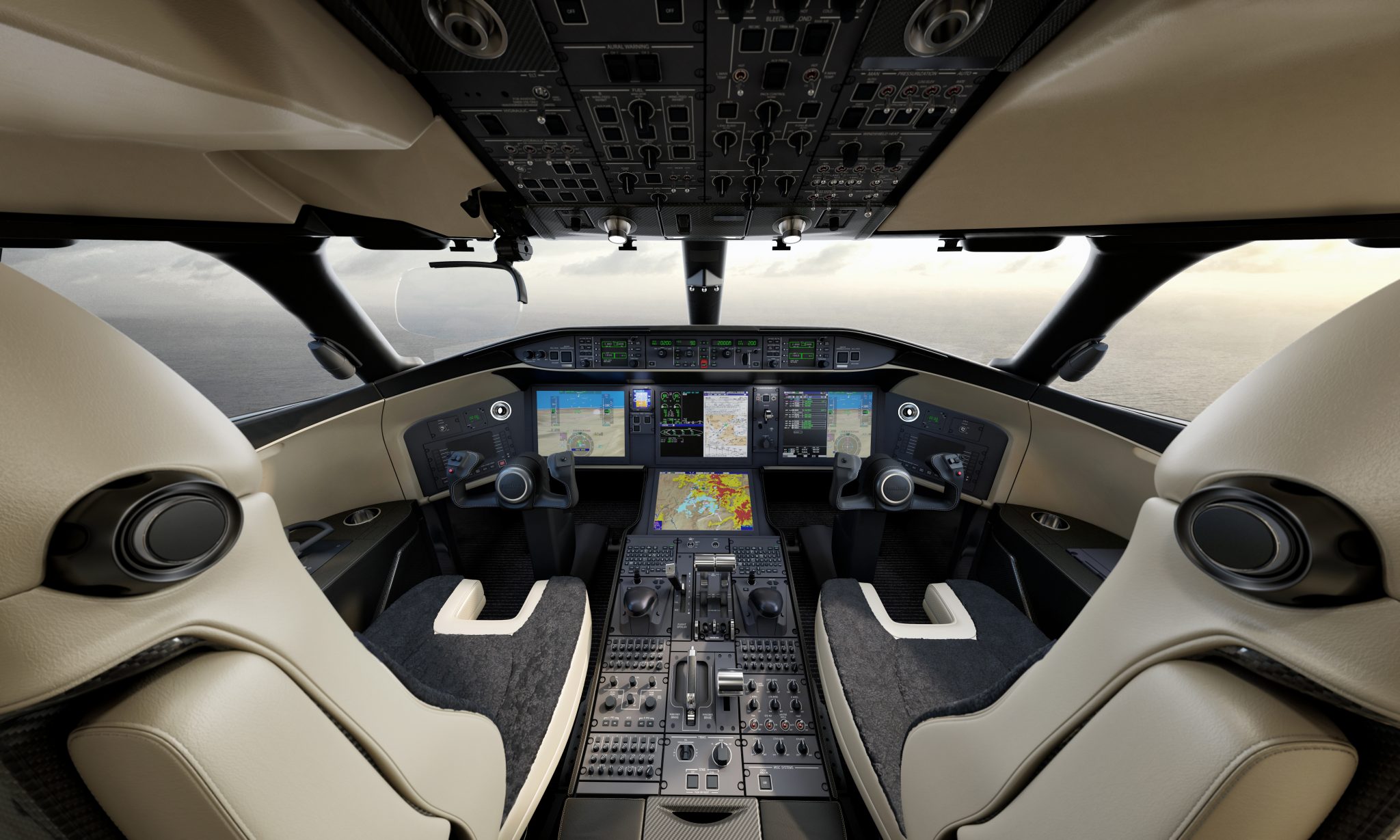
Building trust and reliability in artifical intelligence
In its continuous pursuit of excellence, Bombardier recognizes the sky is the limit. An unrivalled dedication to innovation has propelled the company to the forefront of private aviation. In this ultra-competitive world of business aviation, data and cutting-edge innovation yield industry leading private jets.
Machine learning and Artificial Intelligence (AI) play an important role in aerospace innovation. As the use of AI technologies continues to rise, Bombardier and other manufacturers enjoy the privilege of discovering their immense possibilities and benefits. While AI systems are not novel to the aerospace industry, the introduction of new AI algorithms to perform high-level tasks has prompted the need to ensure these systems are robust and certifiable.
To definitively establish the dependability of new AI and machine learning developments, Bombardier is collaborating in a vast research project, DEEL (DEpendable and Explainable Learning), aimed at maturing AI technologies. The level of trust and dependability in any system must be measured and assessed thoroughly, ensuring total privacy and confidence throughout the system. DEEL focuses on pre-emptively identifying potential vulnerabilities in AI systems to immunize them and ensure their certifiability. Going forward, these advancements and certifications will further cement the future of Bombardier’s excellence by design model.
In the coming years, Bombardier is poised to remain prolific in its high-end market offerings. Bombardier engineers will continue with DEEL researchers to maximize AI-optimized systems to complement and enhance the company’s products and services. On the future of this collaboration, Thomas Reid, Senior Artificial Intelligence engineer at Bombardier’s AI Centre of Excellence, says “whether we think about product improvement or operational efficiency, AI has a big role to play”.